Обратный отсчет нанометров Российский разрабочик рассказывает о мировом рынке процессоров
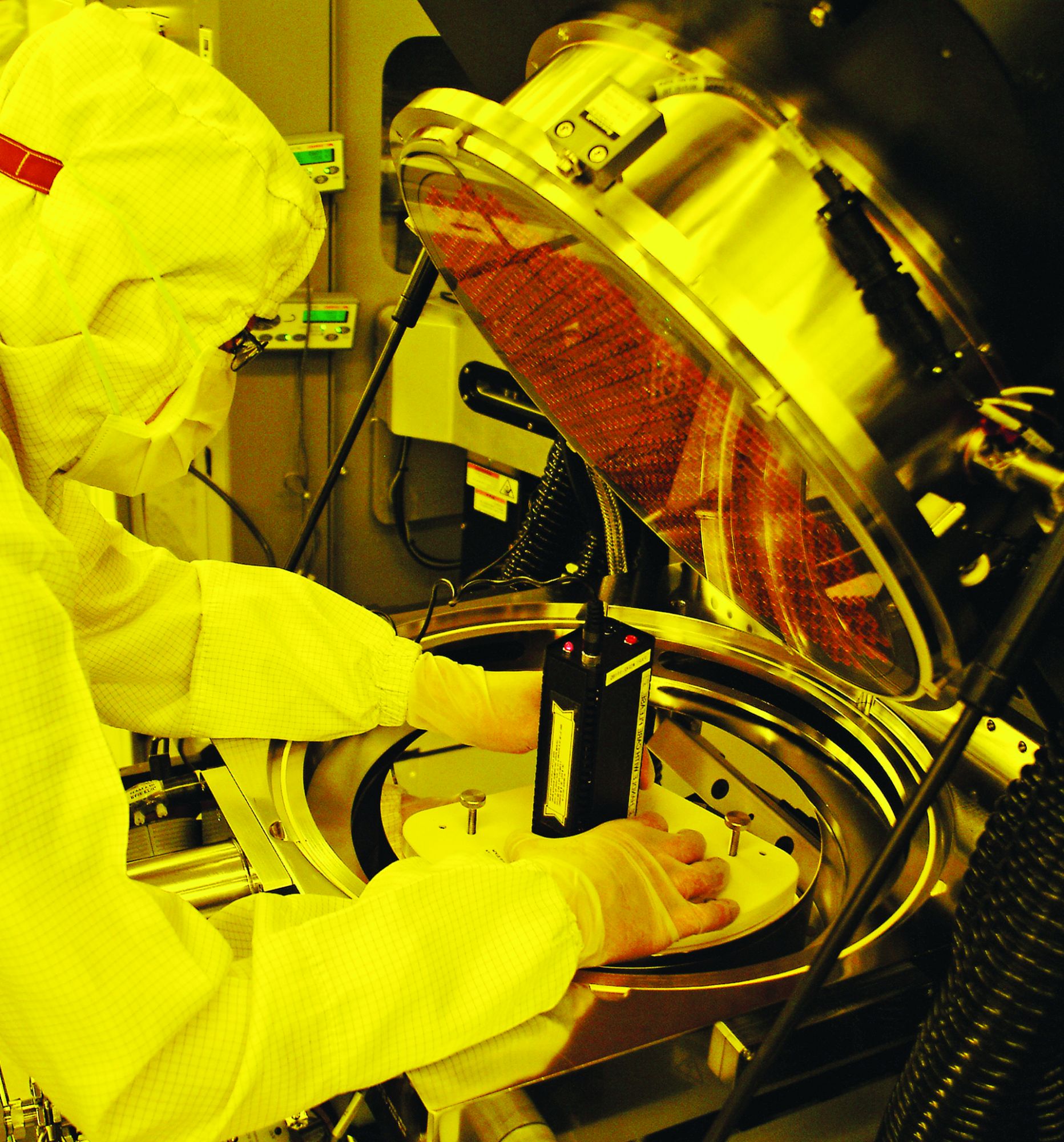
В конце 2020-го в продаже появились устройства с чипами, произведенными по 5-нанометровой технологии. «Закона Мура* нет, но есть тренды развития», — говорит Дмитрий Пустов, вице-президент по маркетингу дизайн-центра процессоров КМ211. Действительно, в современных микросхемах могут быть десятки миллиардов транзисторов*, причем их размеры уменьшились на несколько порядков в сравнении с тем, что было доступно во времена Мура. Такое уменьшение выгодно со всех сторон. Аналогичные по функциям, но более компактные, транзисторы могут плотнее располагаться на микросхеме. Они быстрее срабатывают, меньше нагреваются и расходуют энергии. Именно поэтому «уровень» технологического процесса в микроэлектронике часто оценивают по размерам транзистора, точнее говоря, по самой крошечной детали транзистора, которую этот процесс позволяет произвести.
Эта характеристика не считается строгой и не входит в формальные технические стандарты. «То, что стоит за условными „нанометрами“, не совсем соответствует действительности, — поясняет Дмитрий Пустов. — Точного совпадения между заявленными цифрами и реальностью нет, часто это просто маркетинг». Однако показатель остается удобным и популярным для общей оценки техпроцессов и микросхем. В 1970-х самыми передовыми были микрометровые технологии, а к 2020-му инженеры смогли «ужать» их в тысячи раз. Сегодня массово производятся микрочипы по 10-нанометровому техпроцессу, а с конца 2019-го началось рисковое, «пробное» производство 5-нанометровых.
Задача оказалась под силу далеко не всем. Например, Intel, многолетний флагман мировой микроэлектроники, сбивается с темпа, заданного законом Мура, и до сих пор топчется на границе 10 нм. «За последнее десятилетие они как будто чересчур расслабились, — говорит Дмитрий Пустов. — В результате главными игроками тут оказались Samsung и TSMC». Впрочем, даже этим гигантам было бы не под силу самостоятельно освоить столь сложные технологии. Дело потребовало участия всего мира.
Экстремальный лобзик
Любая микросхема представляет собой сеть из множества транзисторов. Производят их послойно, как если бы мы расставляли ряды стульев снизу вверх: сначала смонтировали все ножки, затем разложили сиденья и, наконец, прикрутили спинки. Каждый слой микросхемы получают из тонкой и плоской пластины кремниевого кристалла, обрабатывая ее лазерным лучом. Процесс называется фотолитографией — «резьбой светом», и это название достаточно точно передает его суть.
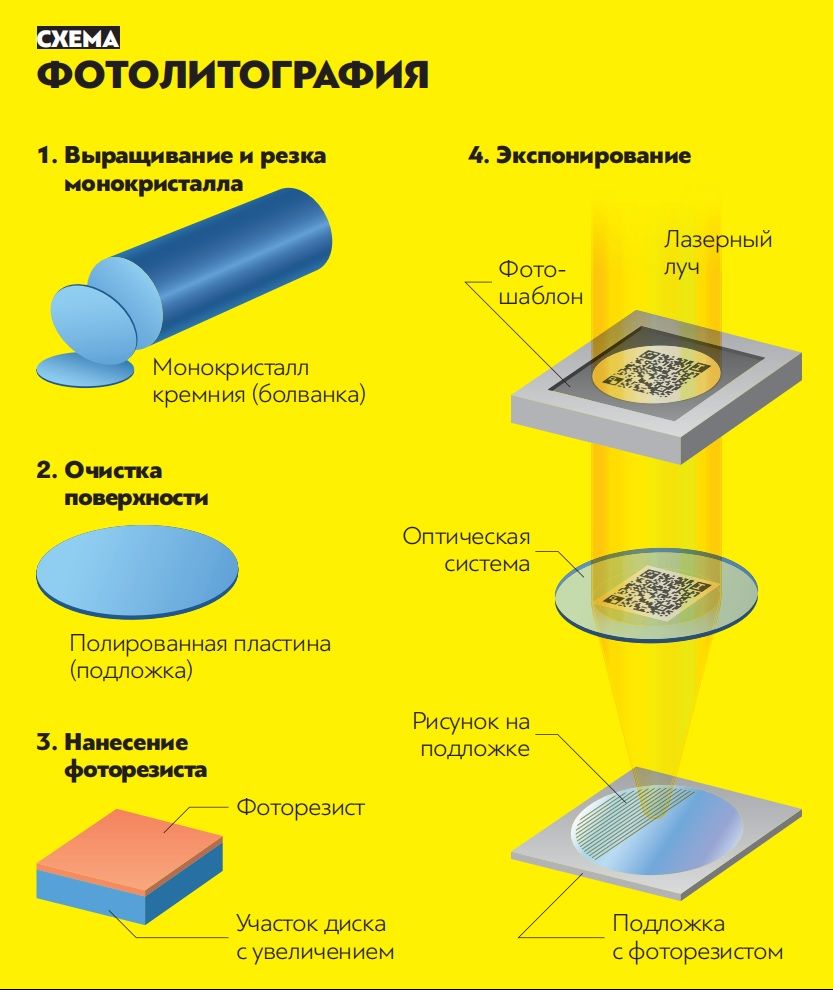
Понятно, что чем мельче детали, которые нужно «вырезать» из пластины, тем тоньше должен быть «лобзик», которым мы работаем. Например, для техпроцессов от 20 нм и ниже применяются аргон-фторовые и аргоновые лазеры с длиной волны 193 и 126 нм соответственно. Но на масштабе 10 и менее нанометров эти инструменты оказываются уже слишком грубыми и не дают нужного разрешения. А лазеров, способных генерировать стабильное и мощное излучение на более коротких волнах, до недавнего времени не существовало. Добиться этого удалось лишь большому международному консорциуму.
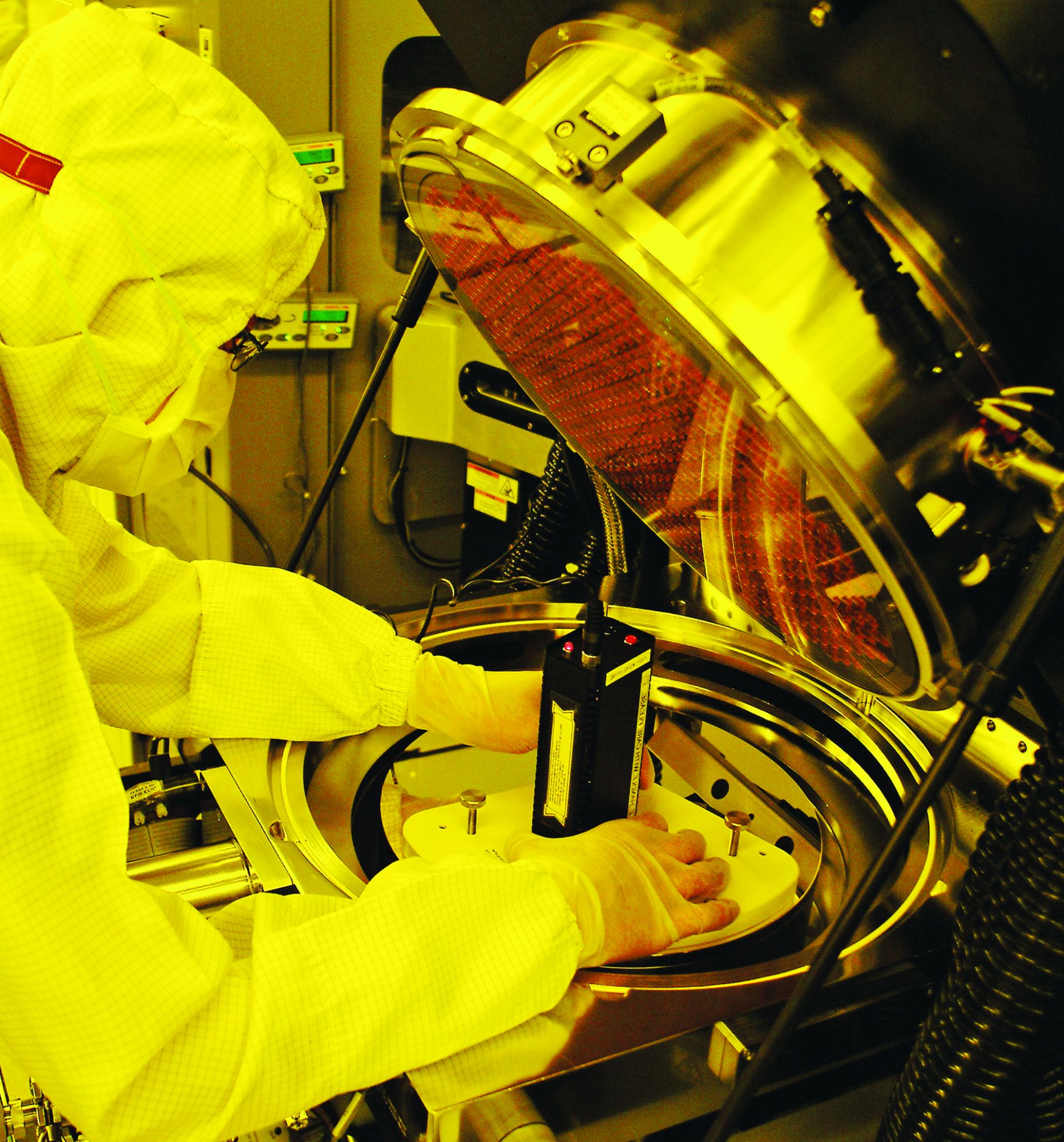
«Первичный» ультрафиолетовый лазер производится американской компанией Cymer. Его луч ударяет в каплю жидкого олова, превращая металл в сгусток плазмы строго определенной формы. Напитавшись энергией, олово переизлучает ее в более коротком диапазоне, около 13 нм, — у самой дальней границы ультрафиолета. Ни одна линза на свете не способна преломлять такие волны, поэтому немецкий концерн Zeiss создал оптическую систему на основе концентрирующих зеркал. А конечный продукт — готовые системы для «экстремальной УФ-литографии» (EUV) — производит нидерландский холдинг ASML. Будучи монополистом, в 2020-м он стоил дороже таких гигантов мировой индустрии, как Airbus или Volkswagen.
Рисковое массовое
Ключевыми покупателями EUV-систем выступают Samsung и TSMC — единственные, кому уже удалось запустить производство микрочипов по 7- и даже 5-нанометровой технологии. Но если южнокорейский концерн работает прежде всего на собственные нужды, то бизнес тайваньской компании построен по противоположной схеме. «Собственных микросхем TSMC не поставляет, занимаясь исключительно производством чужих, — поясняет Дмитрий Пустов. Это позволяет TSMC не конкурировать со своими клиентами, среди которых едва ли не все известные разработчики в мире». Сотрудничает с ними и зеленоградская компания КМ211. «Мы выступаем как независимый дизайн-центр, предлагая услуги по проектированию и производству процессоров, в том числе на мощностях TSMC», — добавляет Дмитрий.
, Вице-президент по маркетингу дизайн-центра КМ211В последние год-два мы, как и другие российские проектировщики, активно развиваем сотрудничество с гражданским сектором. Одни отечественные компании решают создать свои микросхемы в рамках импортозамещения, или же из соображений безопасности. Другим это оказывается дешевле, чем покупать и переделывать под себя чужой продукт. Тем более, что цифровизация экономики нарастает, появляются крупные компании, требующие большого количества микросхем. Соответственно, растет и спрос на проектирование. Но обычно речь идет о менее «нанометровых» процессорах. Они позволяют выполнять большинство практических задач и далеко не так дороги.
Отлаженное производство позволяет фабрикам TSMC обрабатывать порядка 13 миллионов кремниевых пластин в год и постоянно вести модернизацию, вкладывая в разработки по нескольку миллиардов долларов. В 2019-м компания запустила пробное производство на базе 5-нанометрового техпроцесса, а в 2020-м — уже массовое. По ее данным, даже в сравнении с 7 нм это дает выигрыш на 15 % в быстродействии и 30 % в энергопотреблении, а плотность размещения элементов возрастает в 1,8 раза. Первыми в мире «многотиражными» чипами, произведенными по новой технологии, стали кристаллы Apple A14 для iPhone и iPad.
«Запуск нового техпроцесса — это всегда переход на новый уровень сложности, который неизбежно сопряжен с ошибками, — объясняет Дмитрий Пустов. — Лишь со временем технология становится достаточно отработанной, количество дефектов на единицу площади пластины снижается и выходит на плато. Компания переходит от рискового производства — довольно дорогого и с относительно большим количеством брака — к массовому».
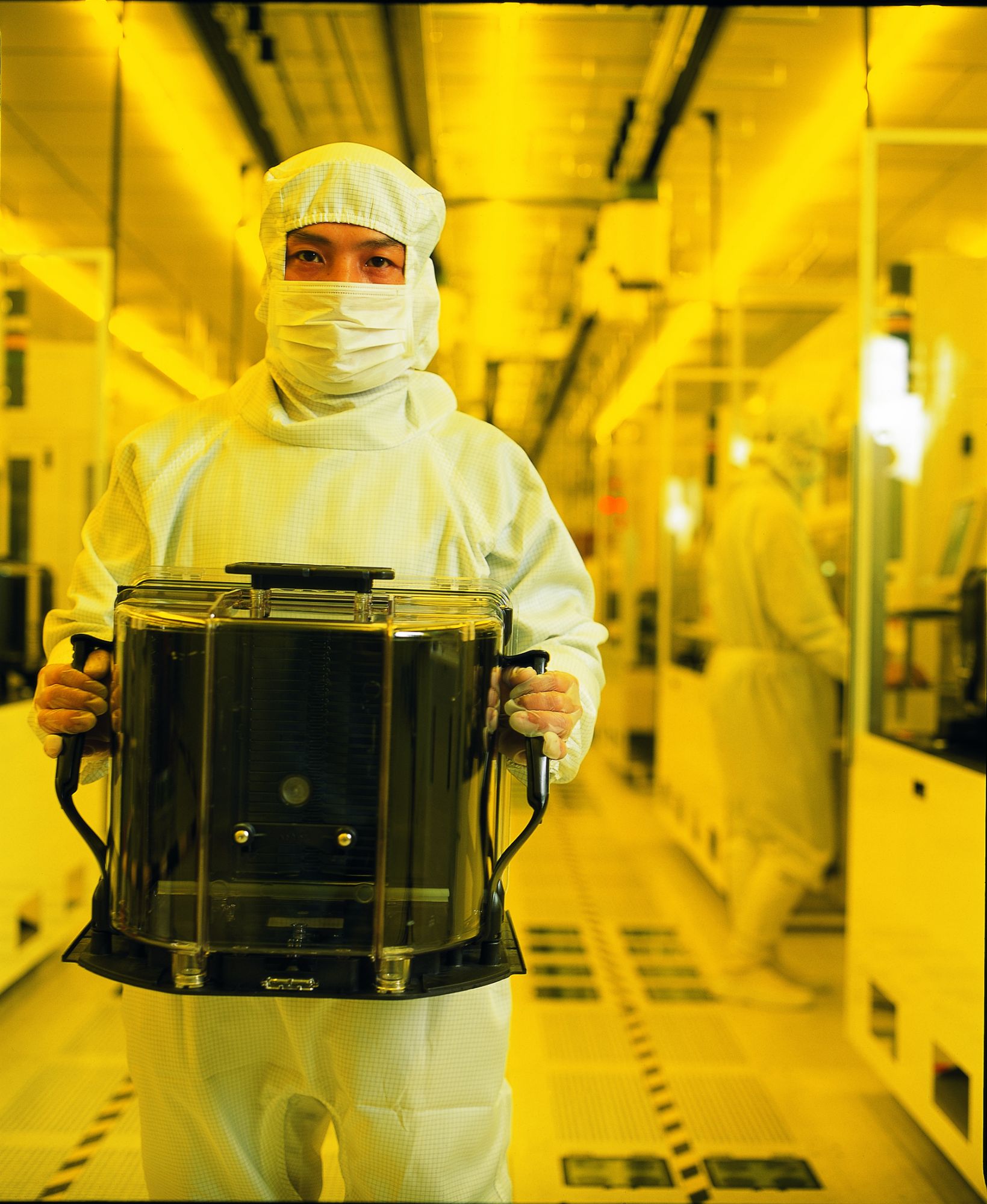
После нанометра
Кажется, что близок физический предел: 1 нм — это диаметр атома водорода, и дальше двигаться просто некуда. Но это лишь на сторонний взгляд. По словам разработчиков из КМ211, следом нас может ожидать новое существенное изменение технологий — например, использование гетеропереходных транзисторов. В таких устройствах кремний сочетается с другими полупроводниками, что повышает их быстродействие даже без уменьшения размеров. «Но если рассуждать о перспективах техпроцессов после 3 нанометров, то тут мы можем только предполагать, — подчеркивает инженер КМ211 Герман Полушкин. — И, как все специалисты, мы предполагаем, что это будут транзисторы из углеродных нанотрубок».
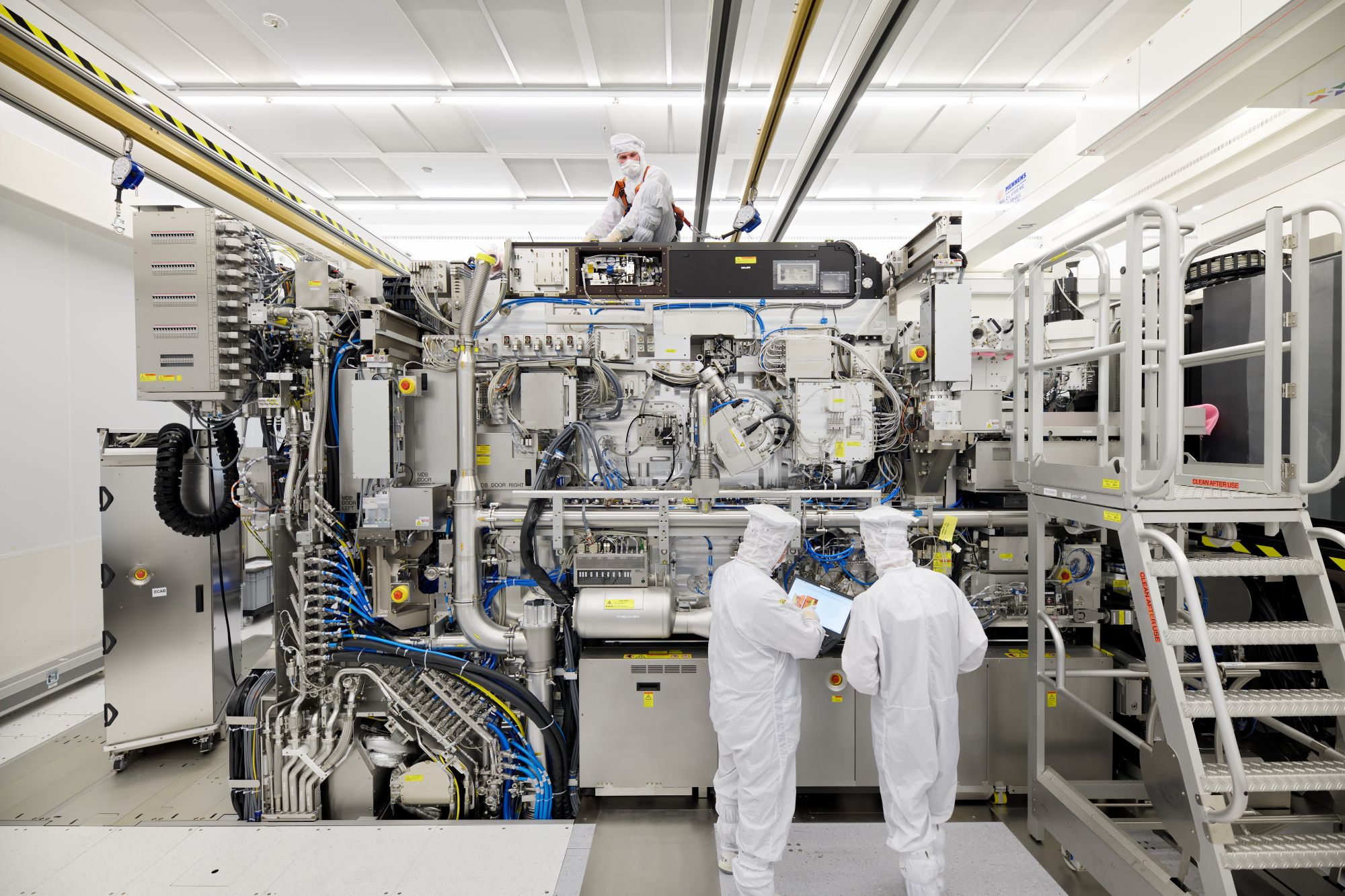
Детали графеновых транзисторов вряд ли станут меньше 1 нм, однако при тех же размерах они дадут новый выигрыш в скорости и энергоэффективности. Углеродные нанотрубки выступают здесь в роли затвора, который контролирует течение тока в транзисторе. Такие системы уже существуют, а в некоторых лабораториях получены и целые микросхемы, построенные на их основе. В 2018 году IBM удалось произвести экспериментальные графеновые микросхемы с помощью слегка видоизмененного фотолитографического процесса. Специалисты полагают, что мы увидим их на массовом рынке на рубеже 2030-х.
Использованные источники: Материал опубликован в журнале «Цифровой океан» № 4, 2021, PaulRaats / ASML, Taiwan Semiconductor Manufacturing Co., Ltd., Bart van Overbeeke, 2019 / ASML, Светлана Зарецкая / FOTOKTOTO.RU
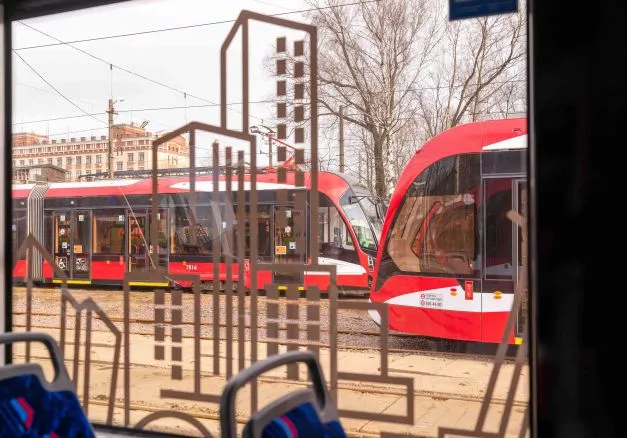